Ideas for Employers: Addressing Workplace Safety & Hazardous Conditions
- Jan 2, 2014
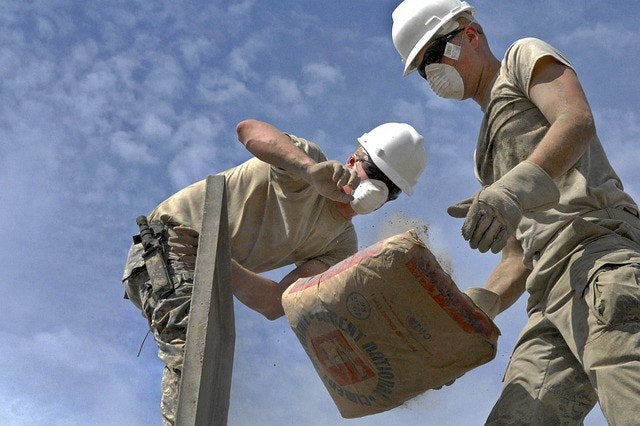
From flagging traffic or performing utility work to concrete work and offshore labor, there are clear and present dangers each and every day. Heavy equipment and highway traffic, power tools and electrical or chemical hazards - there are seemingly endless ways for a person to be seriously injured, disabled or even killed on the job.
While the position and focus on safety differs from job to job, industry to industry and employer to employer, there's on thing that never changes - the importance.
As an employer, you shouldn't assume that the latest equipment and a pamphlet on workplace safety means you're doing everything you can to prevent accidents. Alternatively your employees shouldn't assume that responsibly practicing safety leaves them immune to accidents. No matter how careful they are, there are others on the job as well. If everyone isn't practicing safety they could be putting one another's (as well as the public's) well being, and even lives at risk.
We can't stress this enough because all it takes is one accident to cause a lifetime of problems for employers and employees alike. While all employees like to receive a paycheck and similarly all employers like to see profits, there's a critical level of importance that needs to be placed on properly performing job duties to minimize the chance of an accident.
We've outlined a few ideas below. Read through them and use the information as a starting point or reference, then take the initiative to organize and create your own safety meeting. Make it happen!
Getting Started
Tell your employees that you'd like to schedule a meeting to review safety in the workplace. Give them a few days notice and ask them to make written or mental notes on anything and everything that they see as unsafe, hazardous or generally risky. Your workers often see and/or deal with circumstances that you may not be aware of. Being up front and open about your concern for safety and intention to address any issues lets your employees feel comfortable. Otherwise they might feel like they're criticizing your ownership, managerial skills or competence. You could even tell them that you'd like a list from each employee containing a minimum of 10 potential hazards - this will make them completely comfortable with being forthcoming about any concerns. Encourage them to be creative.
Addressing Workplace Safety Issues
When the time comes, don't make it a rush meeting. You might even want to make a day out of it, or at least an afternoon. Order some food, have some statistics ready (including your company's own safety records) and engage with your employees. Ask them if they feel safe on the job. Ask them if they have concerns. Ask them whether or not they feel that there safety is at risk while they're on the clock at any given time, and why. Dig for answers, discuss all aspects of the job and be sure to cover all of your bases. It might be a good idea to create an outline before the meeting so you can walk through each area of their job duties and ask questions about different scenarios that might occur. Also be sure to ask about any scenarios you might not be aware of or anything you might not have considered.
Take notes of your employee's concerns as well as recommendations for improvement. Ask them for their opinions on the best ways to address these issues. Alternatively, if presenting your own resolutions for improvement be sure ask for their input. Don't automatically assume that you have the best solution - make sure your employees are involved in the process so that issues are resolved to satisfactory standards for everyone.
Based on your industry, you'll have specific safety standards for many things including the manner in which certain duties are performed, what type of protective gear is required or how to properly dispose of certain materials or waste, to name a few. Be sure to talk about these regulations, provide helpful literature and stress the importance of working together. Question them about specific problems that might occur and make sure that they have the knowledge to deal with the situation in a safe manner. Make it clear that practicing safety is a job requirement, just as it's your requirement to provide a safe working environment for them to do so.
Making the Changes and Regrouping
Finally, take action. Make sure these concerns are addressed in a timely fashion and in order of importance, if possible. You've taken the time to initiate a safer workplace so make sure it happens.
Once all safety concerns are in place and have been addressed, have a quick follow up meeting to be sure that nothing has been looked over or forgotten. You'll be glad you did. And be sure to do a verbal pop-quiz on those unexpected circumstances on more time. Even if your employees have undergone vigorous training and testing, it's always good to review safety procedures from time to time.
Your company is only as good as your workers and your workers are only as good as their knowledge allows them to be, so be a good boss and a good employer. Keep them happy & show them that you care about their safety and well being - chances are that they'll be more responsive, appreciative and there will be a better working relationship.